
高爐煤氣脫硫簡介
編輯:2023-01-05 09:50:40
分類:行業新聞
閱讀:90次
本文介紹了(Got it)高爐煤氣精脫硫的(of)基本要(want)求和(and)常規技術路線,重點闡述了(Got it)自主研發的(of)高效水解+高效脫硫技術的(of)工藝流程和(and)技術關鍵與要(want)點,介紹了(Got it)其難點、特點和(and)影響因素,提出(out)了(Got it)高爐煤氣總硫控制、降低SO2排放及實現鋼鐵行業SO2超低排放的(of)有效技術途徑。
高爐煤氣作(do)爲(for)鋼鐵企業産量最大(big)的(of)可燃氣體,其統計産量高達700-800億立方米/月。現有高爐煤氣淨化及後續應用(use)主要(want)是(yes)采用(use)袋式除塵去除顆粒物,再經過TRT餘壓發電後,送往高爐熱風爐、軋鋼加熱爐、煤氣發電等用(use)戶單元作(do)爲(for)燃料使用(use),但高爐煤氣中仍然含有硫、氯等有害物質。随着《關于(At)推進實施鋼鐵行業超低排放的(of)意見》(以(by)下簡稱《意見》)的(of)頒布,鋼鐵行業正式進入“超低排放”時(hour)代,高爐熱風爐、軋鋼加熱爐、煤氣發電等用(use)戶均要(want)求燃燒尾氣SO2達到(arrive)超低排放限值,而現有高爐煤氣淨化流程無法滿足SO2控制要(want)求。目前的(of)技術路線主要(want)包括源頭控制和(and)燃燒後的(of)末端治理,如采用(use)末端治理方式,需在(exist)多點設置脫硫設施,同時(hour),煤氣燃燒後的(of)廢氣量大(big),處理設施規模變大(big);若采取源頭控制方式,實施高爐煤氣精脫硫,減少燃氣中的(of)硫分,可大(big)大(big)降低末端治理的(of)壓力,甚至省掉末端治理設施。
高爐煤氣精脫硫是(yes)一(one)種新的(of)技術發展方向。文獻檢索顯示,單項的(of)有機硫水解技術及幹法吸附脫除技術較多,高爐煤氣脫氯也有相關文獻報道,但未見針對高爐煤氣脫硫或硫分控制技術的(of)報道,也未見高爐煤氣脫硫工程案例的(of)相關報道。焦爐煤氣精脫硫和(and)化工行業CO原料氣脫硫技術及工程案例應用(use)可供參考,但由于(At)高爐煤氣的(of)特殊性,上述技術均不(No)能直接套用(use),因而高爐煤氣精脫硫技術尚屬前沿探索階段。
近年來(Come),随着高爐生(born)産大(big)幅度提高噴煤量和(and)進口礦石比例,高爐煤氣中HCl含量上升,高爐煤氣總管經常出(out)現煤氣管道腐蝕問題。實施高爐煤氣精脫硫可協同處理煤氣中HCl,有效降低煤氣總管腐蝕、洩漏等安全風險。
1高爐煤氣脫硫技術要(want)求
1.1高爐煤氣硫分
高爐煤氣中所含的(of)硫主要(want)分爲(for)有機硫和(and)無機硫兩類,有機硫主要(want)成分有羰基硫、二硫化碳、硫醚硫醇、噻吩等;無機硫主要(want)成分有硫化氫、二氧化硫等。高爐煤氣含硫量及硫分比例與焦炭的(of)硫密切相關,焦炭的(of)全硫、硫形态都可能影響到(arrive)高爐煤氣硫含量。例如,某企業2座同等規模的(of)高爐采用(use)同種原料,對煤氣成分進行監測發現,高爐煤氣硫分波動明顯,監測數據見表1。
對部分鋼鐵企業的(of)監測顯示,高爐煤氣總硫數據多集中在(exist)100-200mg/Nm之間,未見總硫超300mg/Nm的(of)數據。其中有機硫多以(by)羰基硫(COS)爲(for)主,占比約70%;無機硫以(by)硫化氫(H2S)爲(for)主,占比約30%。
上述參數統計僅基于(At)有限的(of)數據調研,并不(No)能作(do)爲(for)所有工程項目的(of)設計依據。針對具體的(of)工程項目,建議應以(by)實測數據爲(for)準。
1.2總硫控制目标
高爐煤氣精脫硫技術對煤氣中總硫控制應以(by)煤氣燃燒後煙氣中SO2達到(arrive)“超低排放”标準要(want)求爲(for)目标。根據《意見》的(of)要(want)求,高爐煤氣的(of)主要(want)用(use)戶煙氣排放SO2控制要(want)求及燃料總硫控制需求計算見表2。
爲(for)便于(At)脫硫系統運行操作(do),高爐煤氣精脫硫裝備宜定期檢驗煤氣中含硫量或安裝連續在(exist)線監測設備,但COS等有機硫組分暫無在(exist)線監測技術及成套設備。鑒此,脫硫系統可使用(use)出(out)口煤氣中H2S含量指标作(do)爲(for)控制參考标準。爲(for)确保高爐煤氣殘餘總硫燃燒後煙氣達到(arrive)SO2超低排放标準,宜取出(out)口煤氣H2S含量≤20mg/Nm3作(do)爲(for)脫硫裝備運行控制數據。
2可選技術路線
高爐煤氣脫硫的(of)關鍵在(exist)于(At)煤氣中羰基硫(COS)的(of)控制與削減。COS是(yes)一(one)個(indivual)結構上與二硫化碳類似的(of)碳化合物,氣态的(of)COS分子爲(for)直線型,COS性質穩定,在(exist)高爐煤氣無氧環境中難于(At)與其他(he)化合物直接發生(born)化學反應,堿液吸收效率較低。工業氣體中脫除COS一(one)般采用(use)先水解再脫硫化氫的(of)方式,硫化氫脫除可使用(use)堿性液吸收法、物理吸附法等。
水解反應式:
1)催化水解
COS H2O→H2S CO2
2)加氫水解
COS 4H2→H2S CH4 H2O
2.1加氫水解+金屬氧化物吸附
該工藝常用(use)于(At)焦爐煤氣精制,焦爐荒煤氣經過化産工段電捕焦油、脫氨、脫硫、脫苯後,H2S含量小于(At)200mg/Nm3的(of)煤氣爲(for)進一(one)步提高品質以(by)提高附加值,可再進行精脫硫。焦爐煤氣精脫硫利用(use)焦爐煤氣中大(big)量的(of)H2,通過催化劑作(do)用(use),将有機硫轉化爲(for)H2S,再通過氧化鐵或氧化鋅吸附劑吸收脫除H2S,達到(arrive)降低焦爐煤氣含硫量的(of)目的(of)。主要(want)流程見圖1。
2.2分子篩或微晶材料吸附
該工藝多用(use)于(At)焦爐煤氣精制,其主要(want)特點在(exist)于(At)解決了(Got it)“加氫水解再吸附”工藝中需要(want)使用(use)兩種物料、多級流程的(of)問題,通過提升物料的(of)比表面積及其對多種硫分的(of)吸附性能,提高吸附傳質速度及硫容等關鍵參數,從而提高脫硫效率。材料吸附飽和(and)後,使用(use)熱煤氣或熱氮氣解吸再生(born),再生(born)煤氣可以(by)回到(arrive)焦爐荒煤氣主管混合後再次經過化産工段淨化其中的(of)硫化氫,再生(born)氮氣則需要(want)另行配套濕式氧化法或濕式吸收法脫除其中的(of)硫化氫。焦爐煤氣吸附吸收法精制工藝見圖2。
2.3小結
上述兩種工藝雖可滿足煤氣中硫分控制從200mg/Nm3降至20mg/Nm3的(of)技術要(want)求,但工程造價過于(At)高昂,以(by)焦爐煤氣精制爲(for)例,僅吸附工段工程造價即達到(arrive)700-900元/Nm3·h,應用(use)于(At)小氣量、高附加值的(of)焦爐煤氣行業尚有一(one)定的(of)經濟價值,若用(use)于(At)低熱值、大(big)氣量的(of)高爐煤氣脫硫,或将給鋼鐵企業帶來(Come)沉重的(of)經濟負擔,不(No)被推薦,也鮮見采用(use)。
3高效水解+高效脫硫技術
爲(for)滿足“鋼鐵行業超低排放”要(want)求,同時(hour)盡量減輕企業的(of)經濟負擔,自主開發了(Got it)針對高爐煤氣總硫控制的(of)專項技術,以(by)較短的(of)工藝流程,很好地(land)适應高爐煤氣工況和(and)高爐運行過程中的(of)煤氣性狀連續突變等複雜條件,并且可持續穩定的(of)達到(arrive)高爐煤氣總硫超低排放的(of)控制目标。
3.1工藝流程簡介
本技術利用(use)煤氣餘壓發電前(TRT)高爐煤氣溫度、壓力較高的(of)有利條件,在(exist)高爐煤氣袋式除塵器後安裝高效水解催化劑,使有機硫與煤氣中殘餘水分發生(born)水解反應而轉化成H2S;高爐煤氣經過TRT降溫減壓後,再采用(use)噴淋空塔脫除煤氣中H2S,達到(arrive)高爐煤氣脫硫的(of)目标。其工藝流程如圖3所示。
3.2技術關鍵及要(want)點
3.2.1水解技術要(want)點
有機硫在(exist)常規金屬氧化物催化作(do)用(use)下如需得到(arrive)較高的(of)COS轉化率,需要(want)低水分、高壓力、高溫度條件,一(one)般要(want)求水解操作(do)溫度爲(for)200℃以(by)上,壓力0.4MPa以(by)上,而高爐煤氣溫度低于(At)200℃,壓力約爲(for)0.2MPa,常規水解工藝和(and)水解催化劑轉化效率迅速衰減。同時(hour),水解催化劑還将受到(arrive)高爐煤氣中其他(he)組分的(of)幹擾,如少量微細顆粒物所含金屬及重金屬元素可能對水解催化劑産生(born)毒害,個(indivual)别市售催化劑在(exist)測試時(hour)甚至短期内即永久性毒化失效。
所開發的(of)高爐煤氣專項水解催化劑和(and)水解工藝可有效減輕上述不(No)利條件的(of)有害影響,并且在(exist)高爐煤氣壓力、溫度條件下穩定地(land)保持80%以(by)上的(of)COS催化水解效率。
3.2.2硫化氫高效脫除技術要(want)點
常規焦爐煤氣H2S脫除爲(for)了(Got it)達到(arrive)更低的(of)出(out)口濃度,多采用(use)低氣速的(of)填料塔型式,以(by)期通過延長停留時(hour)間的(of)方式提高傳質效率,但高爐煤氣産氣量遠高于(At)焦爐煤氣,如果直接采用(use)填料塔型式,則H2S脫除裝備的(of)工程造價将達到(arrive)400-450元/m3·h。如何通過低阻高效的(of)強化傳質措施,在(exist)保證出(out)口H2S控制指标的(of)前提下,盡量縮減設備體量、降低運行阻力,以(by)有限的(of)經濟代價實現高爐煤氣脫硫是(yes)本技術關注的(of)重點。
自主研發的(of)高效噴淋空塔技術在(exist)脫硫塔内集降溫、脫硫、除水于(At)一(one)體,并通過塔内結構的(of)優化設計和(and)脫硫液離子間優化控制等關鍵技術,大(big)幅度提高氣液接觸界面的(of)反應速率,在(exist)較短的(of)停留時(hour)間内,實現更充分有效的(of)傳質,以(by)滿足出(out)口H2S控制指标。與填料塔相比,具有大(big)幅度縮減設備尺寸、節約投資等顯著優點。
3.2.3系統協調
脫硫系統利用(use)了(Got it)高爐煤氣管網的(of)壓力來(Come)克服脫硫裝置的(of)阻力損失,故脫硫系統與高爐生(born)産密切相關。同時(hour),脫硫系統包含的(of)水解工段和(and)噴淋空塔工段對高爐煤氣的(of)溫度、壓力、雜質濃度等參數的(of)波動也比較敏感。通過精細化的(of)工程設計和(and)運行控制,提高脫硫系統對高爐煤氣的(of)适應性,進而減輕或避免對高爐生(born)産的(of)影響也是(yes)本技術考慮的(of)重點和(and)成功的(of)關鍵。
3.2.4其他(he)影響因素
高爐煤氣脫硫系統從進入水解開始到(arrive)離開脫硫塔發生(born)了(Got it)多項化學反應,涉及的(of)傳熱、傳質過程也比較複雜,圍繞着主化學反應的(of)副反應也不(No)少,例如高爐煤氣中HCl會先于(At)H2S與脫硫液反應,雖然實現了(Got it)HCl的(of)協同脫除,但其生(born)成的(of)副鹽富集後又會幹擾H2S的(of)脫除。在(exist)保證主反應充分進行的(of)同時(hour),通過調整脫硫液離子濃度保留必要(want)的(of)副反應,盡量抑制不(No)利副反應發生(born),也是(yes)高爐煤氣脫硫系統連續穩定運行的(of)保障條件。
4結論
1)在(exist)鋼鐵行業“超低排放”的(of)大(big)背景下,高爐煤氣脫硫勢在(exist)必行。
2)實施高爐煤氣精脫硫可大(big)幅度削減鋼鐵行業整體的(of)SO2排放量。
3)自主開發的(of)高爐煤氣脫硫技術具有工藝可靠、低阻高效、運行穩定等顯著特點,可連續穩定運行,滿足高爐煤氣精脫硫的(of)市場需求。
4)應充分認識到(arrive)高爐煤氣脫硫的(of)技術複雜性和(and)難度。針對其多項關鍵技術的(of)研發、優化提升、融合匹配和(and)系統協同運轉等必須有嚴謹的(of)科研态度、認真細緻的(of)工作(do)作(do)風、豐富的(of)工程經驗、強大(big)的(of)工程實力和(and)嚴格規範的(of)工程管理等支撐。
聯系我(I)們(them)
山西威威科技有限公司
聯系人(people):王懷俊
手機:13503518121
微信:13503518121
網址:www.zhiyikj.cn
地(land)址:太原市小店區東崗路259号
郵箱:tywhj@.126.com
在(exist)線留言
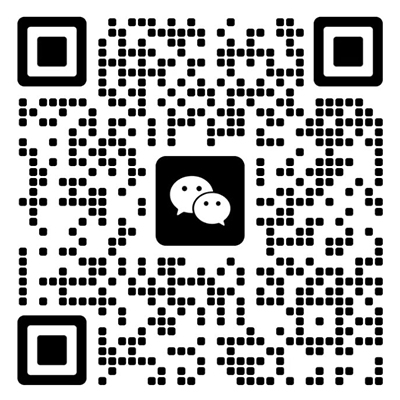
微信掃一(one)掃
版權所有:山西威威科技有限公司 備案号:京ICP證000000号技術支持:龍采科技集團